Silo Engineering
Our in-house experts can help walk you through all the various options and ensure that your concrete silo is built safely, economically, and will last for years to come.
At Marietta Silos, we typically design all of our silos with the assistance of a silo engineer, which fulfills an industry requirement. Our engineering practices fit with the method that our construction crews utilize for our Jumpform and Slipform systems, so it's important to use Marietta Silos for your silo engineering as well as the silo construction.
All of our silos are designed to meet the new silo design code, American Concrete Institute (ACI) 313-16: Design for Concrete Silos and Stacking Tubes for Storing Granular Materials. Marietta Silos is a member of the ACI Committee, keeping our team on the cutting edge of the latest industry standards and updates.
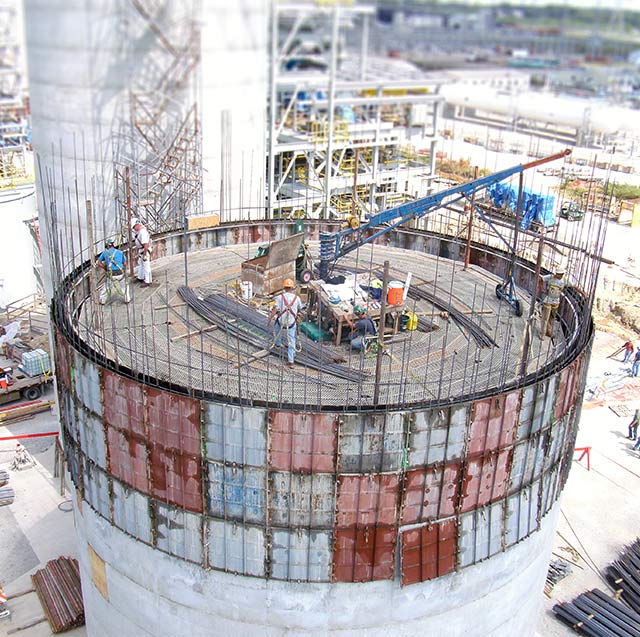
ENGINEERING FOR SILO TYPE
Concrete silos must be designed around the materials they will hold. For instance, cement silos and by-product silos differ greatly in size, wall thickness, cone construction, material handling, equipment, flow patterns, and many other factors.
No matter your silo type, Marietta Silos will help you decide what design is most beneficial for your product and build the best silo to ensure your material's safety.
Aggregate Silos
Aggregate silos have a cone bottom design. The shape of the cone and flow pattern will be specified for the best storage and flow of your aggregate.
Whether you store clay, lime, limestone, sand, gypsum, cement, borax, salt, or any other aggregate, our in-house experts can help walk you through all the design options. We ensure your concrete silo is built safely, economically and will last for years to come.
By-Product Silos
The design of by-product silos will vary depending upon the type of by-product being stored.
Cement Silos
We design and construct silos used for the storage and distribution of various types of cement.
Coal Silos
Experience and knowledge are important in constructing coal silos to guarantee a suitable and economical solution for your needs. Marietta Silos is highly skilled at designing and building silos for soda ash, carbon black, clinker coal and other bulk materials stored in the coal industry. Coal silos generally require a cone bottom with a mass flow to keep the coal moving.
Fly Ash Silos
Marietta Silos is the leading constructor of concrete fly ash silos in the country. We have built more fly ash silos than all our competitors combined. We have earned an unparalleled reputation for excellence through extensive experience with concrete fly ash silos with numerous leading power utilities and contractors throughout the United States. Marietta Silos is also highly experienced in silo building and design for bottom ash and palletized fly ash storage silos.
Grain Silos
Silo construction for flour, grain, or grain product storage provides a sealed silo interior to prevent material spoilage. A demountable silo base allows easy access to remove stored materials.
Lime Silos
Lime silos commonly have a conical hopper in the base of the silo designed to ensure sufficient flow of material through the silo.
CONCRETE SILO FLOW PATTERNS
Materials flow is dependent on a variety of factors. Construction, cone angles, and stored material type all influence how material moves through storage silos.
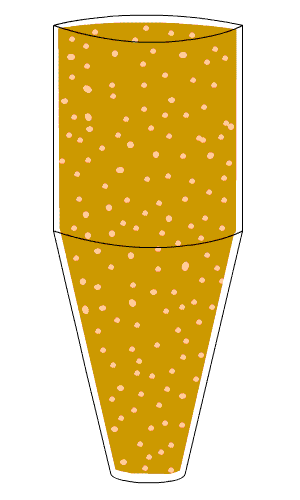
Mass Flow
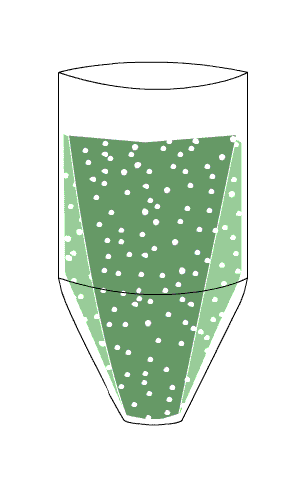
Funnel Flow
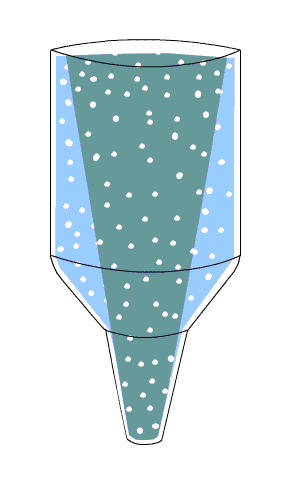
Expanded Flow
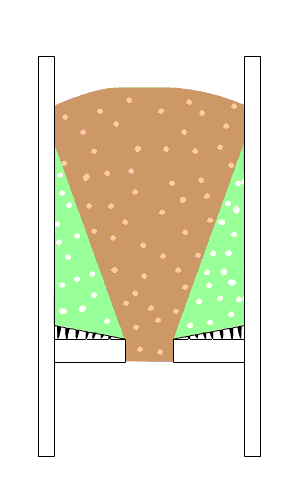
Fluidized Flow
Mass Flow
Mass flow silos do not experience the same potential material flow issues as funnel flow silos. Stored materials move down the silo as a column, with no flow channels, and the first materials in are the first materials out. Mass flow is ideal for materials that are susceptible to segregation based on particle size or density. It is also an ideal flow pattern for coal or other materials that are combustible or perishable. The cone angle used in mass flow silos is between 68-72 degrees, depending on the material being stored and can be lined with a slick material such as stainless steel with a 2B finish.
Funnel Flow
While funnel flow silos are typically more cost-effective to construct, costing between 20-30% less than mass flow silos, they are not suitable for all materials. The flow channel drains material in the middle first. As the silo empties, side material flows into the central channel. Because of this flow pattern, funnel flow silos that are not emptied regularly keep stagnant or dead material against the silo walls. Not emptying the silo causes the material to build up along the silo walls and leads to ratholing or irregular flow issues. Funnel flow silo angles are between 45-60 degrees.
Expanded Flow
Expanded flow is often used in large diameter silos that do not require long-term storage. They provide many benefits of mass flow silos by reducing the potential for ratholing caused by funnel flow in large storage silos. Just as funnel flow silos must be emptied regularly, expanded flow silos benefit from periodic emptying to prevent dead materials buildup. Expanded flow silos feature an interior angle between 45-60 degrees that tapers into a cone angle between 68-72 degrees.
Fluidized Flow
Fluidized flow silos are used for fine powders. A large volume of air pumped into the bottom of the silo aerates stored materials to create a flow pattern similar to fluids. Fluidized flow silos are not suitable for coal storage as the introduction of oxygen can lead to spontaneous combustion. Discharge angles for fluidized flow silos are only between 5-10 degrees.
STACKING TUBES
Stacking tubes generally have their application at coal plants, mines and storage facilities, shipping terminals, and limestone storage. The stacking tube format facilitates an even distribution of coal or limestone into neat piles.
The challenge is to correctly design the tube due to variations in loads applied to them. Loads implied by head houses, conveyor support and belt pull, and asymmetric pile configurations need to be considered during the design. These storage tubes are generally 12' or 14' in diameter; however, in some situations where loading is significantly larger than normal, the diameter may need to increase to accommodate the loading. At the top of the stacking tube, embedded plates are cast to support the conveyor or head house attachments.
The tubes are usually outfitted with 4'x4' mild or stainless-steel window frames that are turned on a 90-degree angle from the bottom to the top of the silo. They are typically 12' apart in a 2x2 alternating arrangement. These tubes are usually erected onto reclaim tunnels. If a stacking tube used for coal storage is erected on top of the tunnel and there is no feeder directly under the center of the tube, an inverted cone will need to be installed at the bottom of the first course of windows. This will prevent stagnant coal from stacking at the bottom of the tube, preventing a spontaneous combustion issue.
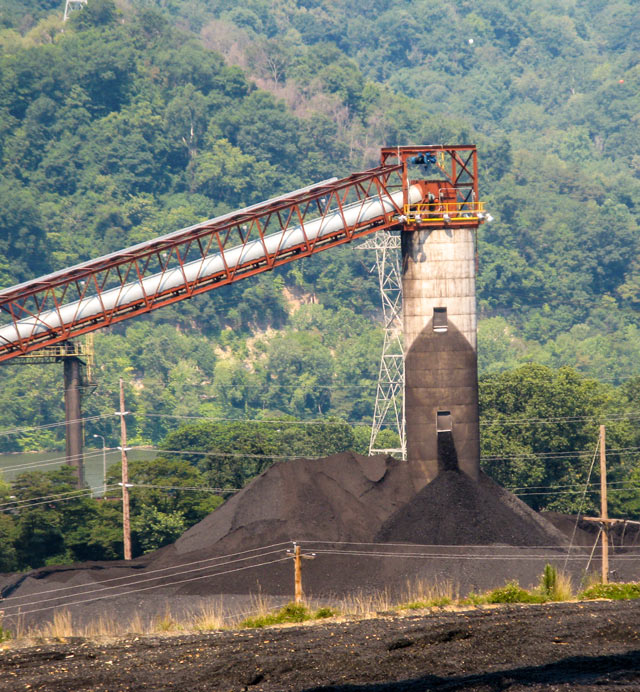
STORAGE SILO SIZING CALCULATORS
Marietta Silos can help you determine the size needed for your silo, the volume for your silo for your specific material type and the best way to store it. Choosing an economic silo size can be a large factor when selecting a silo size. Marietta Silos prefers a 3 to 1 height to diameter ratio, or roughly 90' tall by 30' diameter. If your location is highly seismic, the ratio may drop to a ratio of 2.7/2.8 to 1 to ensure a safer silo design. Marietta Silos recommends that you use this as a guide only, as preliminary designs and sizing can provide a more accurate solution to your specific needs and location. If you need initial designs or sizing, please contact Marietta Silos at 800-633-9969, and we will put you into our priority status of projects.
How a material flows through a silo is very important, as all materials flow at various rates and move through a silo differently. The material flow will determine if you need a flat bottom, cone bottom, funnel flow, mass flow, or expanded flow silo construction. If you are uncertain of the material, how it flows through the silo, or what type of bottom construction you need, a flow study can help determine these aspects. A flow study will take a sample of the material and analyze how it flows, providing you with the information needed to determine your required silo size and type. Marietta Silos can help you get started on a flow design.
Answer a few simple questions, and our silo sizing calculator will give you an estimate of the silo size you need for your materials.