Blog
CATEGORIES
Finding a Long-Term Silo Roof Coating
Silo roof coatings protect both stored materials and the silo itself. Silos experience roof movement cycling and heavy vibration during loading and unloading. This constant movement makes it important to ensure that your silo coating can move with the structure. One of the most common coatings selected by facilities is a membrane coating. While these can be made from rubbers or urethanes, they have several limitations that result in higher long-term expenses.
- Membrane roofs are not designed for any foot traffic as they are easily torn or punctured.
- Ultraviolet light and heat dry out membranes, leaving them brittle.
- Regular frosts and thaws can lead to cracking.
- A short life span necessitates frequent replacements.
- Membranes 'float' above the surface, allowing moisture to spread under the coating and cause unseen damage.
When looking for a silo roof-top coating, high elasticity, direct bond coating products, and resistance to foot traffic provide the greatest ROI with minimal maintenance. Our environmentally-friendly roof-top silo coating adheres directly to the silo surface with a rubberized bond that moves with the silo surface during vibration from loading and unloading and vibrating equipment. This prevents chipping of the roof-top and silo coating and ensures a water-tight seal. In addition, we cover all cracks, holes, equipment attachment points, and penetrations during application to ensure water tightness of your silo.
We start with a base coat that adheres directly to the roofing surface and acts as a filler for small imperfections that could lead to moisture penetration and result in roof failure. We then use a rubberized top coat, which adds durability, resistance to foot traffic, and UV protection. The unique coating can be used on both concrete surfaces and steel.
Take steps today to implement our proven industrial roof coating system. Request a quote from us today.
Following a regular inspection schedule ensures the optimal performance of your silo and can help reduce the liability of unexpected failures. It also helps prevent unplanned downtime from unaddressed issues that slow down production, so you keep to your production schedules.
Regular silo inspections can help identify issues to be addressed before they cause irreparable damage. Larger or more extensive silo damage is inherently more costly, and a silo failure can not only impact neighboring silos it can also lead to loss of life. That's why it's essential to get a regular inspection and then follow through with the recommended repairs.
A professional silo inspection examines several areas that are prone to failure. Depending on the level selected, inspection includes an examination of the silo walls, foundation, cones, and roof, concrete sounding to check for signs of delamination, interior inspection, and, if necessary, services of a senior silo design engineer. It's important to make sure your review is performed by a trained professional as they can identify problems missed by the untrained eye.
The Marietta Silos inspection program is designed to meet the needs of any industry. Our three inspection levels, basic, augmented, and comprehensive, can be combined with our latest supplemental inspection service to give you the highest level of flexibility. The AI Supplemental Inspection service can also be used as a standalone service between regular inspections. Using this service annually, you get an accurate, comprehensive portfolio to better track silo defect changes. The AI Supplemental Inspection service brings silo inspection into the 21st-century through the use of drone capture technology, proprietary software, and artificial intelligence (AI) algorithms that identify even the smallest defects, map precise locations, and rank issues in order of severity. It's also the only service of its kind in the U.S., offered exclusively by Marietta Silos.
Contact us today to schedule a silo inspection. When should you schedule a silo inspection? Watch our video, "How Often Should I Have My Silo Inspected?" for more information on determining silo inspection schedules or view our full library of silo videos on
.
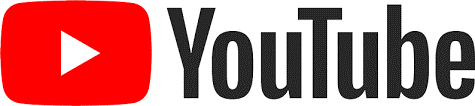
Keeping your silo in good working order starts with a professional inspection. After we have evaluated your silo for both visible and hidden damage, we're able to provide you with a list of necessary maintenance and repairs ranked from most important to least important.
Types of Silo Repair
Marietta Silos offers cleaning, inspection, repair, and maintenance services for concrete and steel silos and bins. As the largest silo repair company in the U.S., we're able to perform both concrete and steel silo repair. The silos we typically service include stave, poured in place, Jumpform, Slipform, bolted steel, and welded steel. Through our extensive experience in all aspects of silo construction and upkeep, we're able to identify and repair problems in silos that are used for a wide range of bulk storage in both agricultural and industrial industries.
Stored Material
- Aggregate
- Borax
- Carbon Black
- Cement
- Clay
- Clinker Coal
- Coal
- Flour
- Fly Ash
- Foundry Sand
- Grain Products
- Gypsum
- Lime
- Palletized Fly Ash
- Salt
- Soda Ash
How You Save
What starts as a minor problem only gets more dangerous and costly to repair as time goes on. It's important to address any signs of silo damage as soon as possible through regular maintenance by a qualified silo repair company. Unaddressed or unknown silo issues jeopardize the quality of stored materials, the silo's structural stability, and the safety of nearby equipment, structures and personnel.
When a silo fails due to lack of maintenance, it can bring production to a halt. The revenue losses from unplanned downtime and the expenses of an emergency repair compound so the overall cost increases substantially. By addressing problems early through regular annual or semi-annual inspections and following through with the prescribed repairs and maintenance, you're able to stick to your production schedule and take care of damages when they are less expensive to repair.
Marietta Silos leads the industry in silo servicing as the only full-service company that addresses all your silo needs under one roof. We offer design, construction, inspection, repair, cleaning, coating, air-pad replacement, vacuum truck service and other maintenance services for various industries. Whether you need silo upgrades, silo strengthening, or other silo repairs - we have the necessary experience and expertise to get the job done correctly.
Contact us today to schedule a silo inspection and your necessary silo repair or learn more about silo maintenance, inspection and repair in our full library of silo videos on
.
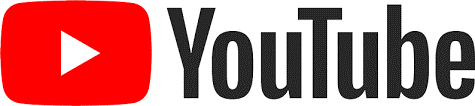